引言:傳統(tǒng)生產(chǎn)的“冰山式浪費(fèi)”
在傳統(tǒng)制造模式中,企業(yè)往往只關(guān)注水面上的顯性成本(如原材料、人工),卻忽視水面下更大的隱性浪費(fèi):
-
數(shù)據(jù)沖擊:全球制造業(yè)平均有效增值時(shí)間僅占生產(chǎn)周期的5%-10%,其余90%以上是等待、搬運(yùn)、返工等非增值活動(dòng);
-
典型案例:某家電企業(yè)年?duì)I收50億,但通過精益診斷發(fā)現(xiàn),僅庫存積壓和過度生產(chǎn)兩項(xiàng),每年吞噬利潤超1.2億。
一、核心理念對(duì)比:兩種生產(chǎn)模式的本質(zhì)差異
傳統(tǒng)生產(chǎn)模式
-
思維邏輯:推動(dòng)式生產(chǎn)(Push System)——“先生產(chǎn)再銷售”
-
核心特征:
-
大規(guī)模批量生產(chǎn),追求設(shè)備利用率最大化
-
部門間各自為政,信息流斷裂
-
依賴經(jīng)驗(yàn)管理,問題解決滯后
精益生產(chǎn)模式
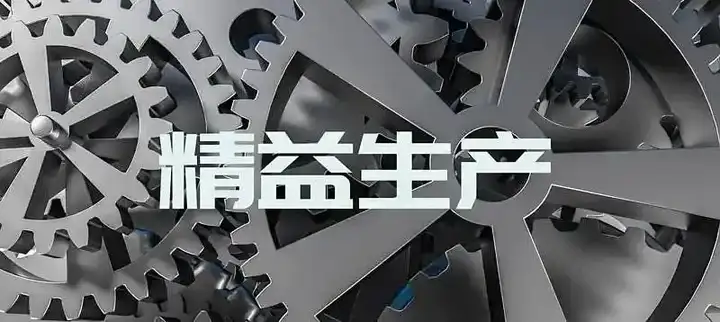
-
思維邏輯:拉動(dòng)式生產(chǎn)(Pull System)——“只生產(chǎn)客戶需要的”
-
核心特征:
-
小批量流動(dòng),按節(jié)拍時(shí)間(Takt Time)精準(zhǔn)匹配需求
-
全流程價(jià)值流透明化,端到端協(xié)同
-
全員參與持續(xù)改善(Kaizen)
▼ 關(guān)鍵差異可視化圖表
二、成本降低30%的五大維度拆解
1. 庫存成本削減:從“資金墳?zāi)埂钡健傲鲃?dòng)血液”
-
傳統(tǒng)痛點(diǎn):某機(jī)械廠倉庫堆滿6個(gè)月用量的螺栓,占用資金800萬
-
精益解法:
-
實(shí)施供應(yīng)商協(xié)同JIT(Just In Time)
-
建立超市拉動(dòng)系統(tǒng)(Kanban),庫存周轉(zhuǎn)率提升3倍
-
量化成果:平均庫存占用減少45%,釋放現(xiàn)金流2600萬/年
2. 質(zhì)量成本歸零:從“救火賠償”到“缺陷預(yù)防”
-
傳統(tǒng)痛點(diǎn):汽車零部件廠因漏裝墊片,批量召回?fù)p失超500萬
-
精益工具:
-
防錯(cuò)設(shè)計(jì)(如扭矩傳感器自動(dòng)報(bào)警)
-
自働化(Jidoka)實(shí)現(xiàn)“零缺陷流出”
-
量化成果:外部故障成本下降72%,年節(jié)省質(zhì)量成本900萬
3. 人工效率提升:從“人海戰(zhàn)術(shù)”到“人機(jī)協(xié)同”
-
傳統(tǒng)痛點(diǎn):電子裝配線30人日產(chǎn)能1200件,步行浪費(fèi)占比38%
-
精益改造:
-
U型單元化布局,步行距離縮短65%
-
多能工培訓(xùn),實(shí)現(xiàn)“一人多序”
-
量化成果:人均產(chǎn)出提升2.1倍,人工成本占比從18%降至11%
4. 能源浪費(fèi)根治:從“粗放消耗”到“精準(zhǔn)管控”
-
傳統(tǒng)痛點(diǎn):注塑車間24小時(shí)開機(jī),空載能耗占35%
-
精益策略:
-
TPM設(shè)備效率分析,識(shí)別待機(jī)浪費(fèi)
-
安裝智能電表+Andon系統(tǒng)實(shí)時(shí)監(jiān)控
-
量化成果:單臺(tái)設(shè)備能耗降低22%,年節(jié)省電費(fèi)超400萬
5. 管理成本壓縮:從“文山會(huì)海”到“現(xiàn)場主義”
-
傳統(tǒng)痛點(diǎn):管理層70%時(shí)間用于開會(huì),卻無法解決產(chǎn)線斷料
-
精益實(shí)踐:
-
實(shí)施Gemba Walk(現(xiàn)場巡查),問題響應(yīng)速度提升5倍
-
可視化看板替代50%會(huì)議
-
量化成果:管理成本占比從12%降至8%,決策周期縮短60%
三、實(shí)戰(zhàn)案例:某上市公司的精益蛻變
企業(yè)背景:國內(nèi)最大衛(wèi)浴五金制造商,年產(chǎn)值28億 改造前:
-
車間在制品堆積高達(dá)15天用量
-
月度客戶投訴超300起
-
綜合毛利率僅19%(行業(yè)平均25%)
精益轉(zhuǎn)型路徑:
-
價(jià)值流分析:鎖定沖壓車間為突破點(diǎn),消除37%非增值步驟
-
快速換模(SMED):模具切換時(shí)間從85分鐘壓縮至9分鐘
-
拉動(dòng)系統(tǒng)建設(shè):建立經(jīng)銷商訂單直連生產(chǎn)系統(tǒng)的數(shù)字看板
成果對(duì)比(12個(gè)月后):
四、實(shí)施路徑:四步啟動(dòng)精益革命
-
價(jià)值流診斷:
-
繪制當(dāng)前狀態(tài)圖(Current State Map)
-
計(jì)算增值比(Value-Added Ratio)
-
速贏機(jī)會(huì)挖掘:
-
優(yōu)先解決“搬運(yùn)距離最長、庫存積壓最多”的環(huán)節(jié)
-
試點(diǎn)突破:
-
選擇1條產(chǎn)線進(jìn)行3個(gè)月試點(diǎn)(忌全面鋪開)
-
文化固化:
-
建立改善提案制度(每月人均≥0.5條)
-
將精益指標(biāo)納入管理層KPI
五、避坑指南:傳統(tǒng)企業(yè)轉(zhuǎn)型三大誤區(qū)
-
誤區(qū)一:重工具輕文化
-
失敗案例:某企業(yè)花200萬買看板系統(tǒng),卻無人更新數(shù)據(jù)
-
對(duì)策:先培養(yǎng)10名內(nèi)部精益教練
-
誤區(qū)二:盲目追求自動(dòng)化
-
失敗案例:自動(dòng)化產(chǎn)線因頻繁換型閑置,ROI為負(fù)
-
對(duì)策:先用精益簡化流程,再自動(dòng)化
-
誤區(qū)三:忽視供應(yīng)鏈協(xié)同
-
失敗案例:內(nèi)部效率提升后,因供應(yīng)商延遲交付再度停產(chǎn)
-
對(duì)策:向關(guān)鍵供應(yīng)商輸出精益方法
結(jié)語:成本戰(zhàn)的終局是價(jià)值戰(zhàn)
精益生產(chǎn)的本質(zhì)不是“壓榨式降本”,而是通過消除浪費(fèi)、加速流動(dòng)、賦能員工,構(gòu)建持續(xù)競爭優(yōu)勢(shì)。當(dāng)傳統(tǒng)企業(yè)還在為5%的成本削減掙扎時(shí),精益先鋒已通過系統(tǒng)性革新實(shí)現(xiàn)30%+的成本重構(gòu)。