6S管理如何讓車間效率翻倍?
一、整理(SEIRI)
整理是 6S 管理的起始點(diǎn),核心在于精準(zhǔn)區(qū)分必需品和非必需品,堅(jiān)決清除非必需品。在車間里,積壓的原材料、損壞的設(shè)備、過期的工具等非必需品大量占用空間,嚴(yán)重阻礙人員與物料的順暢流動。通過整理,將這些物品清理出去,車間空間得以釋放,物料搬運(yùn)路徑大幅縮短,員工能迅速找到所需物品,減少尋找時(shí)間,從而顯著提升工作效率。
比如,某車間在整理前,員工平均每天花費(fèi) 30 分鐘尋找工具和物料,整理后,這一時(shí)間縮短至 5 分鐘,每天節(jié)省出的大量時(shí)間可投入實(shí)際生產(chǎn),效率提升效果立竿見影。
二、整頓(SEITON)
整頓是對整理后的必需品進(jìn)行科學(xué)合理的定位、標(biāo)識和擺放,全面落實(shí) “三定” 原則,即定品、定位、定量。在車間設(shè)置清晰明確的區(qū)域標(biāo)識和物料擺放規(guī)則,每種物料和工具都有固定存放位置,并進(jìn)行醒目標(biāo)識。員工能瞬間找到所需物品,不僅減少尋找時(shí)間,還大幅降低操作失誤。
例如,整頓前物料擺放雜亂無章,員工常常拿錯物料,整頓后,錯誤率大幅降低,生產(chǎn)效率隨之顯著提高。
三、清掃(SEISO)
清掃并非僅僅是表面的打掃衛(wèi)生,更關(guān)鍵的是及時(shí)發(fā)現(xiàn)設(shè)備和工作環(huán)境存在的問題。定期對車間設(shè)備、地面、通道等進(jìn)行全方位清掃,能夠敏銳察覺設(shè)備潛在故障隱患,如松動的零件、異常的磨損、泄漏等。及時(shí)處理這些問題,可有效避免設(shè)備突發(fā)故障導(dǎo)致的生產(chǎn)中斷,有力保證生產(chǎn)的連續(xù)性,進(jìn)而提高生產(chǎn)效率。
比如,某車間通過定期清掃,及時(shí)發(fā)現(xiàn)并修復(fù)設(shè)備潛在問題,設(shè)備故障率從每月 5 次降至 1 次,有效減少生產(chǎn)停機(jī)時(shí)間,保障生產(chǎn)高效進(jìn)行。
四、清潔(SEIKETSU)
清潔是將整理、整頓、清掃工作進(jìn)行制度化、規(guī)范化,形成標(biāo)準(zhǔn)作業(yè)流程并嚴(yán)格執(zhí)行。通過制定詳細(xì)的清潔標(biāo)準(zhǔn)、工作流程和檢查制度,確保車間始終保持整潔、有序的理想狀態(tài)。穩(wěn)定的工作環(huán)境有助于員工養(yǎng)成良好工作習(xí)慣,減少因環(huán)境變化導(dǎo)致的效率波動,持續(xù)推動生產(chǎn)效率提升。
五、素養(yǎng)(SHITSUKE)
素養(yǎng)是 6S 管理的核心與最終目標(biāo),旨在培養(yǎng)員工良好的工作習(xí)慣和職業(yè)素養(yǎng)。通過培訓(xùn)、宣傳和激勵等多種方式,讓員工深刻理解 6S 管理的意義和重要性,自覺遵守 6S 管理規(guī)定。當(dāng)員工具備良好素養(yǎng),會主動維護(hù)車間整潔、有序,積極參與問題解決和持續(xù)改進(jìn),從根本上提升車間整體工作效率。
例如,員工養(yǎng)成定期整理工作區(qū)域、主動報(bào)告設(shè)備問題的習(xí)慣,車間的工作氛圍和效率都會得到顯著提升。
六、安全(SECURITY)
安全是 6S 管理新增且極為重要的一環(huán)。在車間中,完善的安全管理制度、充足的安全防護(hù)設(shè)施以及定期的安全培訓(xùn),能極大降低安全事故發(fā)生概率。一旦發(fā)生安全事故,不僅會導(dǎo)致人員傷亡,還會使生產(chǎn)被迫中斷,造成設(shè)備損壞、物料浪費(fèi)等損失,嚴(yán)重影響生產(chǎn)效率。通過加強(qiáng)安全管理,如設(shè)置明顯的安全警示標(biāo)識、定期檢查設(shè)備安全性能、開展安全應(yīng)急演練等,可有效預(yù)防事故發(fā)生。員工在安全的環(huán)境中工作,能夠更加專注,無需擔(dān)憂安全問題而分心,從而提高工作效率。
例如,某車間加強(qiáng)安全管理后,安全事故發(fā)生率降為零,員工工作效率提升了 20%,同時(shí)因避免事故損失節(jié)省了大量成本。
綜上所述,6S 管理通過整理、整頓、清掃、清潔、素養(yǎng)和安全這六個(gè)方面協(xié)同作用,從優(yōu)化工作環(huán)境、規(guī)范員工行為、保障生產(chǎn)安全等多維度入手,為車間效率翻倍提供有力支撐,全面提升車間的生產(chǎn)效率、產(chǎn)品質(zhì)量和員工工作狀態(tài)。
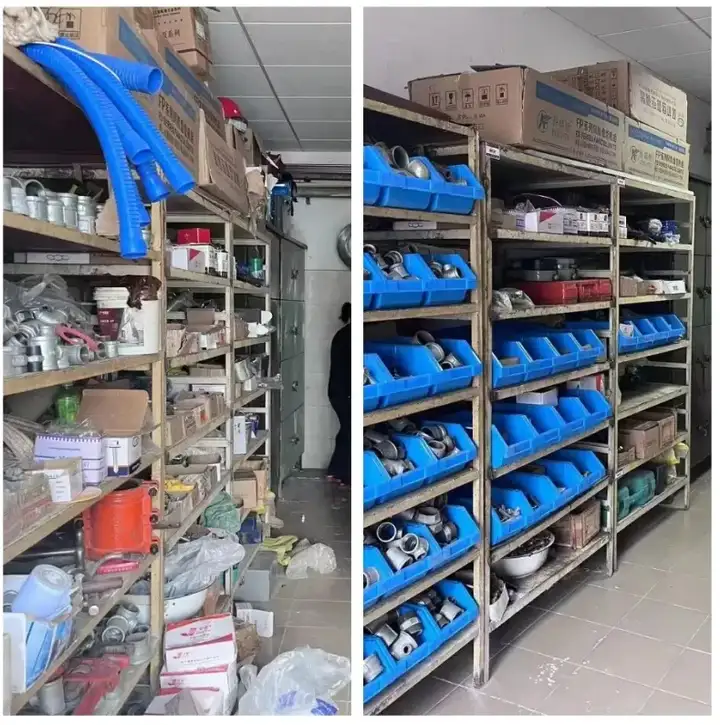
6S 管理在不同行業(yè)車間中的應(yīng)用效果
汽車制造行業(yè):以豐田汽車車間為例
豐田汽車車間全面推行 5S 管理,在整理環(huán)節(jié),清理掉生產(chǎn)線旁長期積壓的零部件和工具,釋放出近 20% 的生產(chǎn)空間,物料搬運(yùn)距離平均縮短了 30 米。整頓階段,對各類零部件和工具實(shí)施 “三定” 管理,員工尋找所需物品的時(shí)間從平均每次 5 分鐘縮短至 1 分鐘以內(nèi),裝配效率大幅提升。通過嚴(yán)格的清掃制度,及時(shí)發(fā)現(xiàn)并解決設(shè)備隱患,設(shè)備故障率降低了 40%,有效減少了因設(shè)備故障導(dǎo)致的停產(chǎn)時(shí)間。清潔工作的制度化讓車間始終保持最佳狀態(tài),員工工作失誤率下降了 30%。長期的素養(yǎng)培育,使員工主動參與改進(jìn),提出的合理化建議數(shù)量增長了 50%,推動生產(chǎn)效率持續(xù)提升,產(chǎn)品質(zhì)量也更加穩(wěn)定。
電子裝配行業(yè):某知名電子企業(yè)車間
該電子企業(yè)車間在推行 6S 管理后,整理掉大量廢舊電子元件和閑置設(shè)備,使車間空間利用率提高了 15%。整頓工作規(guī)范了電子元件的擺放和取用流程,員工操作失誤率降低了 40%,裝配效率提高了 35%。清掃過程中,及時(shí)發(fā)現(xiàn)靜電隱患并加以解決,產(chǎn)品不良率從 3% 降至 1.5%。清潔的常態(tài)化保障了生產(chǎn)環(huán)境的穩(wěn)定,生產(chǎn)效率波動控制在 5% 以內(nèi)。員工素養(yǎng)的提升,讓團(tuán)隊(duì)協(xié)作更加順暢,整體生產(chǎn)效率提升了 40% 以上。
食品加工行業(yè):某大型食品加工廠車間
在食品加工車間,整理環(huán)節(jié)清理了過期原料和雜物,避免了交叉污染風(fēng)險(xiǎn),食品安全事故發(fā)生率降低了 60%。整頓后,原料和工具擺放有序,生產(chǎn)流程更加順暢,加工效率提高了 30%。嚴(yán)格的清掃和清潔措施,使車間衛(wèi)生狀況達(dá)到更高標(biāo)準(zhǔn),產(chǎn)品抽檢合格率從 85% 提升至 95%。員工素養(yǎng)的提升,使其更加注重食品安全和衛(wèi)生,主動遵守操作規(guī)范,產(chǎn)品質(zhì)量投訴率下降了 70%,生產(chǎn)效率穩(wěn)步提升。
通過這些不同行業(yè)的案例可以看出,6S 管理在車間中具有廣泛的適用性和顯著的成效,能夠有效提升車間的生產(chǎn)效率、產(chǎn)品質(zhì)量和員工素養(yǎng)。