在當(dāng)下風(fēng)云變幻的商業(yè)戰(zhàn)場中,企業(yè)們都在絞盡腦汁,尋覓提升效率、削減成本的秘訣。
精益生產(chǎn),這一備受推崇的高效生產(chǎn)理念,宛如一盞明燈,照亮了眾多企業(yè)前行的道路。
然而,你是否知曉,在日常生產(chǎn)流程的 “隱秘角落”,潛藏著諸多不易察覺的浪費(fèi),它們恰似潛伏在暗處的 “利潤竊賊”,悄無聲息地侵蝕著企業(yè)的競爭力。
今天,就讓我們一同撥開迷霧,深入探尋精益生產(chǎn)中的八大浪費(fèi)類型,并研究如何將這些 “攔路虎” 逐一清除。
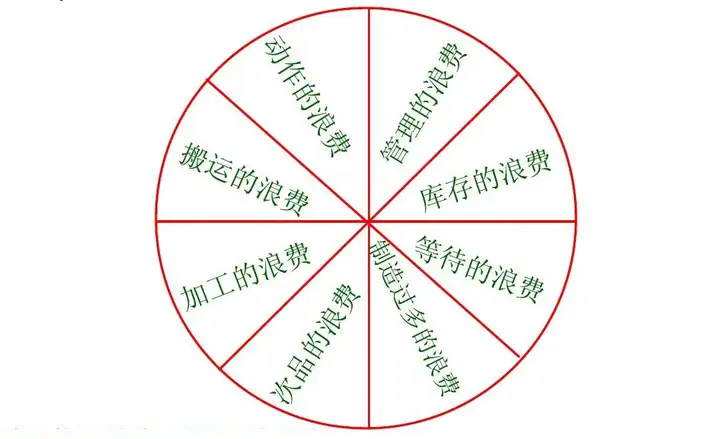
1、過量生產(chǎn)的浪費(fèi):囤貨如山,得不償失
過量生產(chǎn)堪稱生產(chǎn)界的 “囤貨狂魔”。想象一下,有一家服裝企業(yè),滿心期待著旺季訂單如潮水般涌來,于是在淡季便火力全開,瘋狂趕制服裝??僧?dāng)旺季的喧囂漸漸褪去,倉庫里卻堆積如山,滿是滯銷的衣物。
這些過剩的庫存,不僅占用了大量寶貴資金,還霸占了額外的倉儲空間。更為糟糕的是,隨著時間的無情流逝,服裝款式迅速過時,無奈之下,只能大幅打折促銷,甚至直接報廢處理,企業(yè)損失慘重。
豐田汽車在發(fā)展早期,也曾深陷這一困境。彼時,過度生產(chǎn)的汽車積壓成災(zāi),資金與場地被大量占用。
后來,豐田果斷引入準(zhǔn)時化生產(chǎn)(JIT)理念,精準(zhǔn)依據(jù)客戶訂單來安排生產(chǎn),只有在接到訂單后,才開始生產(chǎn)相應(yīng)數(shù)量的汽車。這一舉措成效顯著,成功甩掉了過量生產(chǎn)的沉重包袱,資金周轉(zhuǎn)率大幅提升,如同裝上了強(qiáng)勁的動力引擎。
企業(yè)若想擺脫過量生產(chǎn)的桎梏,需構(gòu)建一個精準(zhǔn)如 “神算子” 般的需求預(yù)測系統(tǒng),時刻與客戶保持緊密溝通,敏銳捕捉市場需求的細(xì)微變化。
同時,果斷切換至拉動式生產(chǎn)模式,讓客戶訂單成為指揮生產(chǎn)的 “指揮官”,而非僅憑主觀臆測盲目生產(chǎn)。
2、等待的浪費(fèi):干瞪眼的損失
在生產(chǎn)線上,工人們常常會陷入 “干瞪眼” 的無奈境地。原材料供應(yīng)不及時,他們只能百無聊賴地等待材料到位,才能繼續(xù)手頭的工作;設(shè)備突發(fā)故障,維修期間整個生產(chǎn)線瞬間停滯,員工們只能無所事事,白白浪費(fèi)時間。
有家電子組裝廠就深受其擾,供應(yīng)商送貨總是 “慢悠悠”,每個月生產(chǎn)線都會因等待原材料而停工數(shù)小時。
這一停工,不僅浪費(fèi)了工人的寶貴工作時間,還嚴(yán)重打亂了整個生產(chǎn)計劃的節(jié)奏。后來,該廠與供應(yīng)商重新 “約法三章”,明確了送貨時間,并搭建了庫存預(yù)警系統(tǒng),一旦庫存低于安全線,便能及時補(bǔ)貨。
這一系列舉措,成功大幅縮短了生產(chǎn)線的等待時間,生產(chǎn)效率直線攀升。
要消除等待的浪費(fèi),企業(yè)必須精心優(yōu)化供應(yīng)鏈管理,與供應(yīng)商建立牢不可破的緊密合作關(guān)系,確保原材料按時、按量送達(dá)。
同時,強(qiáng)化設(shè)備的維護(hù)保養(yǎng)工作,制定完備的設(shè)備故障應(yīng)急預(yù)案,最大程度縮短設(shè)備故障停機(jī)時間。此外,合理規(guī)劃生產(chǎn)流程,杜絕工序之間的銜接不暢,減少等待情況的發(fā)生。
3、運(yùn)輸?shù)睦速M(fèi):冤枉路,冤枉錢
物料和產(chǎn)品在不必要的搬運(yùn)與運(yùn)輸過程中,同樣會造成驚人的浪費(fèi)。例如,有的工廠布局宛如一座錯綜復(fù)雜的 “迷宮”,原材料從倉庫運(yùn)往生產(chǎn)車間,需歷經(jīng)多個迂回曲折的路線,這不僅耗費(fèi)大量時間與人力,運(yùn)輸途中物料還極易受損。
某汽車制造企業(yè)曾面臨這樣的難題,工廠內(nèi)零部件運(yùn)輸距離過長,導(dǎo)致運(yùn)輸成本居高不下,效率卻極為低下。
于是,他們痛下決心,對工廠布局進(jìn)行了大刀闊斧的重新規(guī)劃,將相關(guān)工序和設(shè)備緊密安置在一起,零部件的運(yùn)輸路程大幅縮短。同時,引入先進(jìn)的自動導(dǎo)引車(AGV),實(shí)現(xiàn)了物料運(yùn)輸?shù)淖詣踊?,運(yùn)輸成本和時間雙雙大幅降低。
企業(yè)可借鑒這家汽車制造企業(yè)的經(jīng)驗,對工廠布局來一場徹底的 “大變身”,將生產(chǎn)流程相關(guān)環(huán)節(jié)盡可能靠攏,減少物料搬運(yùn)的冤枉路。積極采用先進(jìn)的物流設(shè)備和技術(shù),讓運(yùn)輸效率實(shí)現(xiàn)質(zhì)的飛躍,降低運(yùn)輸途中的損耗。
4、庫存的浪費(fèi):囤貨的代價
除了過量生產(chǎn)引發(fā)的庫存積壓,不合理的庫存管理同樣是個 “吞金巨獸”。過多的原材料庫存,意味著大量資金被死死占用,而且隨著存放時間的增加,庫存物資極有可能變質(zhì)、損壞。
一家食品加工廠,為防止原材料短缺影響生產(chǎn),大量囤積面粉、糖等原材料。結(jié)果,部分原材料因存放時間過久,受潮變質(zhì),只能忍痛丟棄。
后來,該廠引入庫存管理系統(tǒng),依據(jù)生產(chǎn)計劃精準(zhǔn)計算原材料需求量和采購時間,將庫存維持在合理水平,既有效避免了缺貨風(fēng)險,又顯著減少了庫存浪費(fèi)。
企業(yè)應(yīng)運(yùn)用科學(xué)的庫存管理方法,比如借助 ABC 分類法對庫存物資進(jìn)行分類管理,重點(diǎn)關(guān)注價值高、用量大的物資。同時,與供應(yīng)商建立高效的快速補(bǔ)貨機(jī)制,朝著低庫存甚至零庫存生產(chǎn)的目標(biāo)穩(wěn)步邁進(jìn)。
5、加工的浪費(fèi):多此一舉的損耗
加工過程中,如果工藝不合理或者過度加工,同樣是在白白浪費(fèi)資源。比如某機(jī)械加工廠在生產(chǎn)零件時,采用了極為復(fù)雜的加工工藝,雖說能保證零件質(zhì)量,但耗費(fèi)的時間和能源多得驚人,生產(chǎn)成本也隨之直線上升。
一家家具廠也遇到過類似狀況,在木材加工環(huán)節(jié),部分工人為確保產(chǎn)品質(zhì)量,對木材進(jìn)行過度打磨,遠(yuǎn)超實(shí)際需求標(biāo)準(zhǔn)。這不僅浪費(fèi)了大量人力和時間,砂紙等耗材的使用量也大幅增加。
后來,該廠對加工工藝進(jìn)行優(yōu)化,制定了清晰明確的加工標(biāo)準(zhǔn)和操作規(guī)范,工人嚴(yán)格按照標(biāo)準(zhǔn)操作,產(chǎn)品質(zhì)量得以保證,加工浪費(fèi)也大幅減少。
企業(yè)要定期對生產(chǎn)工藝進(jìn)行全面評估和優(yōu)化,剔除不必要的加工步驟,積極采用先進(jìn)的加工技術(shù)和設(shè)備,提升加工效率和質(zhì)量,降低加工成本。
6、動作的浪費(fèi):無效忙碌的消耗
在車間里,工人一些不必要的動作也會造成浪費(fèi)。比如,工人在操作過程中頻繁彎腰去拿工具,或是轉(zhuǎn)身尋找物料,這些多余的動作不僅耗費(fèi)體力,還延長了作業(yè)時間。
有一家玩具廠,工人在組裝玩具時,工具擺放雜亂無章,每次拿取工具都要花費(fèi)不少時間尋找。后來,工廠重新設(shè)計了工作臺,將常用工具按照操作順序整齊擺放,工人伸手就能拿到所需工具,減少了無效動作,工作效率明顯提高。
要消除動作的浪費(fèi),企業(yè)需要對工作場所進(jìn)行合理布局,根據(jù)操作流程優(yōu)化工具和物料的擺放位置,讓工人能夠以最便捷的方式完成工作,減少不必要的動作。同時,開展員工培訓(xùn),讓他們掌握高效的工作動作規(guī)范,提高操作效率。
7、不良品的浪費(fèi):瑕疵帶來的損失
生產(chǎn)過程中出現(xiàn)不良品,意味著之前投入的人力、物力、財力都打了水漂。一家手機(jī)組裝廠,由于部分零部件質(zhì)量不過關(guān)以及組裝工藝問題,生產(chǎn)出了一批有屏幕顯示故障的手機(jī)。
這些不良品不僅需要返工維修,耗費(fèi)額外的人力和時間,嚴(yán)重的甚至只能報廢處理。后來,該廠加強(qiáng)了對原材料供應(yīng)商的質(zhì)量管控,引入先進(jìn)的檢測設(shè)備,在生產(chǎn)過程中增加多道質(zhì)量檢測工序,從源頭減少不良品的產(chǎn)生,降低了因不良品造成的損失。
企業(yè)要建立完善的質(zhì)量管理體系,從原材料采購、生產(chǎn)過程到成品檢驗,每一個環(huán)節(jié)都嚴(yán)格把控質(zhì)量。加強(qiáng)對員工的質(zhì)量意識培訓(xùn),讓他們明白質(zhì)量的重要性,同時采用先進(jìn)的質(zhì)量檢測技術(shù)和設(shè)備,及時發(fā)現(xiàn)和解決質(zhì)量問題,減少不良品的浪費(fèi)。
8、管理的浪費(fèi):無序管理的代價
管理不善同樣會導(dǎo)致大量浪費(fèi)。例如,企業(yè)內(nèi)部信息溝通不暢,部門之間協(xié)調(diào)不到位,就會出現(xiàn)重復(fù)工作、決策延誤等問題。
一家制造企業(yè),市場部門接到客戶訂單后,未能及時準(zhǔn)確地將訂單信息傳達(dá)給生產(chǎn)部門,導(dǎo)致生產(chǎn)部門按照舊的生產(chǎn)計劃進(jìn)行生產(chǎn),生產(chǎn)出來的產(chǎn)品不符合客戶需求,只能重新生產(chǎn),造成了極大的浪費(fèi)。
后來,該企業(yè)引入了信息化管理系統(tǒng),實(shí)現(xiàn)了部門之間信息的實(shí)時共享和快速傳遞,同時優(yōu)化了工作流程,明確了各部門職責(zé),有效減少了管理上的浪費(fèi)。
企業(yè)要建立科學(xué)合理的管理制度和流程,明確各部門和崗位的職責(zé),加強(qiáng)信息溝通與協(xié)作。利用信息化手段提高管理效率,實(shí)現(xiàn)資源的優(yōu)化配置,避免因管理混亂而產(chǎn)生的浪費(fèi)。
精益生產(chǎn)中的這八大浪費(fèi),如同隱藏在企業(yè)內(nèi)部的 “蛀蟲”,持續(xù)侵蝕著企業(yè)的效益和競爭力。
但只要我們精準(zhǔn)識別并全力消除這些浪費(fèi),企業(yè)便能實(shí)現(xiàn)生產(chǎn)效率的飛躍、成本的有效降低,在激烈的市場競爭中脫穎而出。
記住,消除浪費(fèi),就是為企業(yè)創(chuàng)造價值;減少一分浪費(fèi),就多一分企業(yè)的未來。讓我們攜手踏上精益生產(chǎn)的變革征程,為企業(yè)鑄就輝煌的明天。