當(dāng)特斯拉上海超級工廠實現(xiàn)從鋼板到整車下線僅需45小時的制造速度,當(dāng)豐田九州工廠每百臺車質(zhì)檢問題數(shù)僅為行業(yè)平均值的1/8,這些數(shù)字背后都指向同一個底層邏輯——精益生產(chǎn)的系統(tǒng)化實踐。
本文深度解析全球五大汽車巨頭的精益轉(zhuǎn)型路徑,揭示傳統(tǒng)制造業(yè)突破成本困局、實現(xiàn)價值躍遷的實戰(zhàn)方法論。
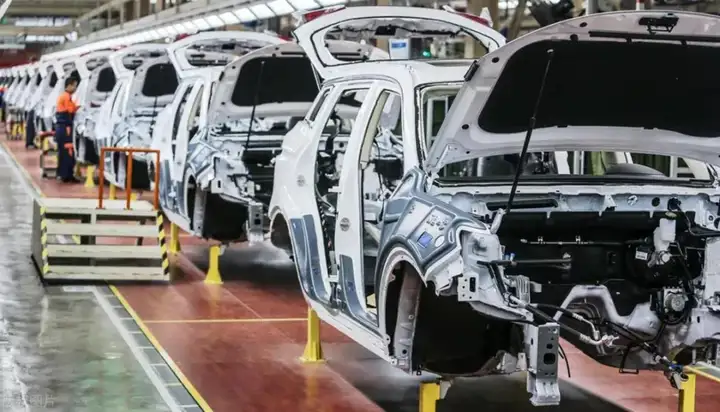
一、豐田TPS進化論:從消除浪費到創(chuàng)造價值流
九州宮田工廠的零缺陷革命 作為雷克薩斯核心生產(chǎn)基地,該工廠將傳統(tǒng)七大浪費擴展至"第8大浪費——知識浪費",構(gòu)建三層防御體系:
-
工序級防錯:發(fā)動機裝配線配置267個傳感器,實時監(jiān)測螺栓扭矩、密封膠厚度等23項參數(shù)
-
系統(tǒng)級攔截:通過MES系統(tǒng)比對工序履歷,發(fā)現(xiàn)未執(zhí)行檢測工序自動鎖止移載機
-
組織級保障:建立"質(zhì)量道場"培訓(xùn)體系,新員工需完成200小時缺陷情景模擬訓(xùn)練
成果:整車Audit評審分值提升至98.7分,質(zhì)量成本占比降至0.8%(行業(yè)平均2.3%)
供應(yīng)鏈協(xié)同創(chuàng)新 開發(fā)供應(yīng)商協(xié)同平臺(SCP),實現(xiàn):
-
零部件庫存周轉(zhuǎn)率從15次/年提升至36次
-
模具切換時間通過共享設(shè)備利用率數(shù)據(jù)降低42%
-
建立成本透明化的"價值工程聯(lián)盟",年度降本達采購額3.2%
二、大眾MQB平臺的模塊化奇跡
平臺化生產(chǎn)的成本重構(gòu) 通過模塊化橫向矩陣設(shè)計,大眾實現(xiàn):
-
開發(fā)成本降低20%,零件通用率提升至70%
-
產(chǎn)線切換時間從56小時壓縮至8小時
-
單臺制造成本下降€1200
沃爾夫斯堡工廠的數(shù)字化精益
-
應(yīng)用數(shù)字孿生技術(shù)模擬生產(chǎn)線,設(shè)備布局效率提升19%
-
AGV物流系統(tǒng)與生產(chǎn)節(jié)拍實時聯(lián)動,在制品庫存降低63%
-
工人佩戴AR眼鏡指導(dǎo)復(fù)雜裝配,培訓(xùn)周期縮短75%
三、特斯拉的一體化壓鑄技術(shù)革命
上海超級工廠的成本顛覆 采用6000噸級Giga Press壓鑄機:
-
將70個零件整合為1個整體鑄件,焊接點從800個減至50個
-
車身產(chǎn)線長度縮短35%,廠房面積節(jié)省20%
-
單件制造成本降低30%,缺陷率下降40%
生產(chǎn)節(jié)拍同步系統(tǒng)
-
電池車間與總裝車間通過智能配送系統(tǒng)實現(xiàn)秒級響應(yīng)
-
采用激光雷達掃描技術(shù),將車身匹配精度控制在±0.1mm
-
建立"問題作戰(zhàn)室",異常停線時間縮短至4.3分鐘/日
四、吉利汽車的數(shù)字化轉(zhuǎn)型路徑
春曉基地的智能柔性產(chǎn)線
-
配置217臺協(xié)作機器人,實現(xiàn)5款車型混流生產(chǎn)
-
通過視覺檢測系統(tǒng)自動識別3000種零部件
-
開發(fā)工藝大數(shù)據(jù)平臺,將換模時間壓縮至行業(yè)平均值的1/3
供應(yīng)鏈穿透式管理
-
構(gòu)建四級供應(yīng)商可視化系統(tǒng),風(fēng)險預(yù)警提前7天
-
實施VMI庫存共享計劃,周轉(zhuǎn)率提升至18次/年
-
與寧德時代共建"產(chǎn)能銀行",實現(xiàn)電池供應(yīng)動態(tài)調(diào)節(jié)
五、福特鋁車身精益化突破
F-150皮卡生產(chǎn)的價值流再造
-
采用軍用級鋁合金替代鋼材,重量減輕320kg
-
開發(fā)電磁沖壓技術(shù),將車門板生產(chǎn)工序從8道減至2道
-
建立閉環(huán)鋁材回收系統(tǒng),材料利用率達92%
魯日中心的零距離布局
-
將沖壓、焊裝、涂裝車間直線距離壓縮至300米
-
應(yīng)用數(shù)字墨水技術(shù),實現(xiàn)個性化訂單實時排產(chǎn)
-
推行"三現(xiàn)主義"(現(xiàn)場/現(xiàn)物/現(xiàn)實),管理層每日4小時現(xiàn)場巡查
(戰(zhàn)略級啟示)
這些案例揭示汽車行業(yè)精益轉(zhuǎn)型的三大趨勢:
-
技術(shù)穿透:從工業(yè)工程向數(shù)字工程躍遷,IoT+AI構(gòu)建實時價值流
-
系統(tǒng)重構(gòu):打破組織邊界,構(gòu)建"研發(fā)-制造-供應(yīng)鏈"一體化作戰(zhàn)體系
-
人機共融:將員工智慧轉(zhuǎn)化為算法邏輯,實現(xiàn)持續(xù)改善的永動機制
正如豐田生產(chǎn)系統(tǒng)創(chuàng)始人大野耐一所言:"精益不是一套工具,而是培養(yǎng)能發(fā)現(xiàn)浪費的眼睛。"當(dāng)中國新能源汽車滲透率突破40%的今天,精益生產(chǎn)正在從成本控制手段進化為價值創(chuàng)造引擎,這場制造業(yè)的"靜默革命",將決定未來十年全球汽車產(chǎn)業(yè)的競爭格局。