在工廠生產(chǎn)的舞臺上,設(shè)備就是主角,它們一旦 “鬧脾氣” 發(fā)生故障,整個生產(chǎn)流程就可能陷入混亂。而精準(zhǔn)找出設(shè)備故障的根源,就如同為生病的主角診斷病因,是恢復(fù)生產(chǎn)秩序的關(guān)鍵。今天,我們就來聊聊在設(shè)備故障根因分析中極為有效的 TPM 方法。
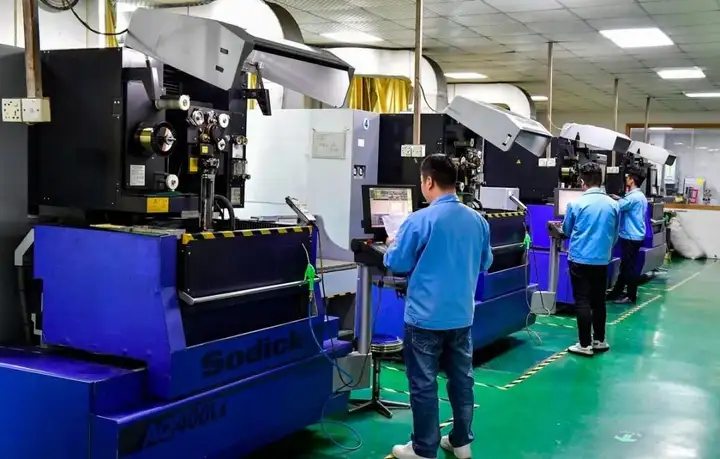
一、TPM 方法:全面生產(chǎn)維護(hù)的智慧結(jié)晶
TPM,即 Total Productive Maintenance,全面生產(chǎn)維護(hù),它倡導(dǎo)全員參與,從設(shè)備的規(guī)劃、設(shè)計、使用到維護(hù)的全生命周期進(jìn)行管理,旨在追求設(shè)備綜合效率最大化。
在設(shè)備故障根因分析領(lǐng)域,TPM 方法憑借其系統(tǒng)性和全面性,成為眾多企業(yè)的得力助手。
TPM 方法強(qiáng)調(diào)預(yù)防為主,通過日常的設(shè)備檢查、清潔、潤滑、緊固等保養(yǎng)工作,及時發(fā)現(xiàn)設(shè)備潛在問題,將故障隱患扼殺在萌芽狀態(tài)。同時,當(dāng)故障不幸發(fā)生時,TPM 也提供了一套科學(xué)嚴(yán)謹(jǐn)?shù)姆治隽鞒?,幫助我們抽絲剝繭,找到故障的真正根源。
二、TPM 方法在設(shè)備故障根因分析中的實(shí)戰(zhàn)應(yīng)用
案例一:某汽車零部件加工廠
在一家汽車零部件加工廠,一臺關(guān)鍵的沖壓設(shè)備頻繁出現(xiàn)沖壓件尺寸偏差的問題。起初,維修人員只是簡單地調(diào)整設(shè)備參數(shù),但問題依舊反復(fù)出現(xiàn)。后來,該廠引入 TPM 方法進(jìn)行故障根因分析。
首先,成立了由設(shè)備操作人員、維修人員、工藝工程師組成的 TPM 小組。小組成員通過對設(shè)備運(yùn)行數(shù)據(jù)的詳細(xì)記錄和觀察,發(fā)現(xiàn)設(shè)備在運(yùn)行一段時間后,沖壓模具的溫度會異常升高。
進(jìn)一步檢查發(fā)現(xiàn),模具的冷卻系統(tǒng)存在堵塞,冷卻液流通不暢,導(dǎo)致模具溫度過高,進(jìn)而影響沖壓件尺寸。
找到問題根源后,TPM 小組一方面對冷卻系統(tǒng)進(jìn)行全面清理和維護(hù),確保冷卻液正常循環(huán);另一方面,制定了嚴(yán)格的設(shè)備日常檢查制度,要求操作人員每班都要檢查冷卻系統(tǒng)的運(yùn)行狀況。實(shí)施這些措施后,沖壓設(shè)備的故障發(fā)生率大幅降低,產(chǎn)品質(zhì)量得到了顯著提升。
案例二:電子制造企業(yè)的 SMT 生產(chǎn)線
一家電子制造企業(yè)的 SMT 生產(chǎn)線經(jīng)常出現(xiàn)貼片機(jī)拋料現(xiàn)象,嚴(yán)重影響生產(chǎn)效率。企業(yè)運(yùn)用 TPM 方法展開深入分析。
TPM 小組成員從人、機(jī)、料、法、環(huán)五個方面入手。在人員方面,檢查操作人員的操作規(guī)范,發(fā)現(xiàn)部分新員工對設(shè)備操作不夠熟練,在更換物料時動作不規(guī)范,容易導(dǎo)致物料偏移,從而引發(fā)拋料。
在設(shè)備方面,對貼片機(jī)進(jìn)行全面檢查,發(fā)現(xiàn)吸嘴磨損嚴(yán)重,影響了對物料的吸取精度。
在物料方面,經(jīng)過檢驗(yàn),發(fā)現(xiàn)部分物料的包裝不符合標(biāo)準(zhǔn),導(dǎo)致物料在送料過程中出現(xiàn)卡頓。
在方法方面,優(yōu)化了貼片機(jī)的編程參數(shù),使其更適應(yīng)不同類型物料的貼裝要求。
在環(huán)境方面,改善了車間的溫濕度控制,避免因環(huán)境因素影響物料的性能。
通過對這些問題的逐一解決,SMT 生產(chǎn)線的拋料率從原來的 5% 降低到了 1% 以內(nèi),生產(chǎn)效率大幅提高。
三、TPM 方法應(yīng)用的關(guān)鍵要點(diǎn)
-
全員參與:TPM 強(qiáng)調(diào)全員參與,只有操作人員、維修人員、管理人員等各部門人員共同協(xié)作,才能全面收集設(shè)備信息,準(zhǔn)確找出故障根因。
-
數(shù)據(jù)收集與分析:詳細(xì)記錄設(shè)備運(yùn)行數(shù)據(jù),包括溫度、壓力、轉(zhuǎn)速等,以及故障發(fā)生時的具體情況,通過對這些數(shù)據(jù)的深入分析,為故障根因判斷提供有力依據(jù)。
-
持續(xù)改進(jìn):設(shè)備故障根因分析不是一勞永逸的,企業(yè)要根據(jù)實(shí)際情況,不斷優(yōu)化 TPM 方法的應(yīng)用,持續(xù)改進(jìn)設(shè)備管理水平。
在設(shè)備故障根因分析的道路上,TPM方法為我們點(diǎn)亮了一盞明燈。它以其科學(xué)的理念和實(shí)用的方法,幫助企業(yè)快速、準(zhǔn)確地找出設(shè)備故障根源,提升設(shè)備運(yùn)行效率,保障生產(chǎn)的順利進(jìn)行。