一、成本降低的隱形戰(zhàn)場
2025年1月,某家電巨頭因?qū)嵤?a href="http://lxshy.cn" target="_blank" rel="noopener noreferrer">持續(xù)改善項(xiàng)目,年度成本降低12.3億元,利潤率提升4.7%。這一數(shù)據(jù)背后,揭示了一個被長期忽視的真相:持續(xù)改善不是短期行為,而是長期成本降低的戰(zhàn)略引擎。
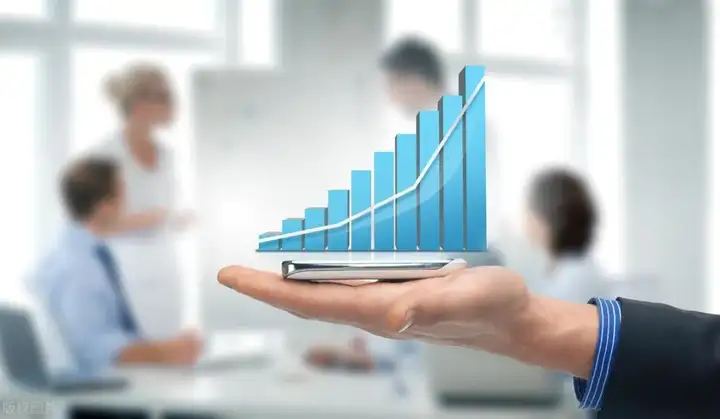
數(shù)據(jù)震撼:
-
全球制造業(yè)因持續(xù)改善帶來的成本節(jié)約年均超1200億美元(《2025全球制造業(yè)成本白皮書》)
-
精益標(biāo)桿企業(yè)通過持續(xù)改善,生產(chǎn)成本年均降低8%-12%(麥肯錫研究報(bào)告)
-
某汽車零部件企業(yè)通過改善活動,單件成本下降23%,年節(jié)約成本超5億元
二、持續(xù)改善的四大降本邏輯
1. 消除浪費(fèi):從顯性到隱性
-
七大浪費(fèi)的數(shù)字化識別:
? 過量生產(chǎn):通過智能排程減少庫存積壓(某電子廠庫存周轉(zhuǎn)率提升3倍)
? 等待時間:通過實(shí)時監(jiān)控減少設(shè)備閑置(某機(jī)械廠設(shè)備利用率提升至92%)
? 運(yùn)輸浪費(fèi):通過優(yōu)化布局減少物流距離(某食品廠物流成本下降18%) -
隱性浪費(fèi)的量化分析:
? 動作浪費(fèi):通過動作分析減少無效操作(某裝配線效率提升35%)
? 管理浪費(fèi):通過流程優(yōu)化減少審批環(huán)節(jié)(某化工企業(yè)審批周期縮短60%)
2. 流程優(yōu)化:從局部到全局
-
價(jià)值流圖(VSM)的應(yīng)用:
? 識別瓶頸工序:某汽車廠通過VSM分析,將生產(chǎn)周期從12天縮短至7天
? 優(yōu)化信息流:某電子廠通過信息化改造,訂單交付周期縮短40% -
全流程協(xié)同改善:
? 跨部門協(xié)作:某家電企業(yè)通過跨部門改善小組,將新品開發(fā)周期縮短30%
? 供應(yīng)鏈協(xié)同:某機(jī)械廠通過供應(yīng)商協(xié)同改善,采購成本下降15%
3. 技術(shù)創(chuàng)新:從傳統(tǒng)到智能
-
數(shù)字化工具的引入:
? 數(shù)字孿生:某航空企業(yè)通過虛擬調(diào)試,減少80%的試制返工
? 人工智能:某制藥廠通過AI預(yù)測性維護(hù),設(shè)備故障率下降60% -
自動化與智能化升級:
? 機(jī)器人應(yīng)用:某電子廠通過自動化改造,人工成本下降25%
? 智能檢測:某汽車廠通過AI視覺檢測,漏檢率降至0.01%
4. 文化驅(qū)動:從被動到主動
-
全員參與的改善文化:
? 改善提案制度:某化工企業(yè)年人均提案數(shù)達(dá)12件,累計(jì)節(jié)約成本1.2億元
? 改善激勵機(jī)制:某機(jī)械廠通過積分獎勵,改善項(xiàng)目完成率提升至95% -
持續(xù)學(xué)習(xí)的組織能力:
? 精益培訓(xùn)體系:某電子廠通過系統(tǒng)培訓(xùn),培養(yǎng)精益骨干200人
? 知識管理平臺:某汽車廠通過知識庫建設(shè),改善經(jīng)驗(yàn)共享效率提升50%
三、持續(xù)改善的長期價(jià)值
1. 成本結(jié)構(gòu)的根本性優(yōu)化
-
從"降本"到"價(jià)值創(chuàng)造":通過持續(xù)改善,企業(yè)不僅降低現(xiàn)有成本,還能優(yōu)化成本結(jié)構(gòu),提升長期競爭力
-
案例:某家電企業(yè)通過改善活動,將研發(fā)成本占比從12%降至8%,同時新產(chǎn)品上市周期縮短30%
2. 組織能力的持續(xù)提升
-
從"改善項(xiàng)目"到"改善基因":持續(xù)改善不僅帶來成本節(jié)約,還能培養(yǎng)組織的自我優(yōu)化能力
-
案例:某汽車零部件企業(yè)通過持續(xù)改善,年人均效率提升15%,員工流失率下降20%
3. 市場競爭力的持續(xù)增強(qiáng)
-
從"價(jià)格競爭"到"價(jià)值競爭":通過持續(xù)改善,企業(yè)不僅能降低成本,還能提升產(chǎn)品價(jià)值,增強(qiáng)市場競爭力
-
案例:某機(jī)械廠通過改善活動,將產(chǎn)品不良率降至0.1%,客戶滿意度提升至98%
四、實(shí)戰(zhàn)案例:豐田的"改善基因"
-
痛點(diǎn):傳統(tǒng)生產(chǎn)模式下,成本居高不下,市場競爭力不足
-
創(chuàng)新方案:
-
建立全員參與的改善文化,年人均提案數(shù)達(dá)10件
-
引入數(shù)字化工具,實(shí)現(xiàn)全流程的實(shí)時監(jiān)控與優(yōu)化
-
成果:
? 生產(chǎn)成本年均降低8%-12%
? 產(chǎn)品不良率降至0.05%
? 市場占有率提升至25%
五、行動路線圖
-
立即行動:建立持續(xù)改善的組織架構(gòu),明確目標(biāo)與責(zé)任
-
技術(shù)升級:2025年內(nèi)完成關(guān)鍵工序的數(shù)字化改造(推薦SAP Lean Management平臺)
-
文化驅(qū)動:開展全員參與的改善活動,建立激勵機(jī)制
-
持續(xù)優(yōu)化:建立改善效果的評估體系,持續(xù)優(yōu)化改善流程
未來已來:當(dāng)持續(xù)改善成為組織的基因,當(dāng)每一名員工都成為改善的推動者,這場關(guān)乎制造業(yè)生死的隱形戰(zhàn)爭,正在重新定義成本競爭的底層規(guī)則。