在全球制造業(yè)競爭白熱化的今天,日本豐田通過精益生產(chǎn)實現(xiàn)人均產(chǎn)值達德國大眾的2.3倍,美國波音公司應(yīng)用精益方法將飛機裝配周期縮短30%。這些數(shù)據(jù)揭示:掌握精益生產(chǎn)的核心策略,不僅能顯著降低成本,更能建立可持續(xù)的競爭優(yōu)勢。
本文系統(tǒng)梳理十大經(jīng)過驗證的精益策略,為企業(yè)提供可落地的降本路線圖。
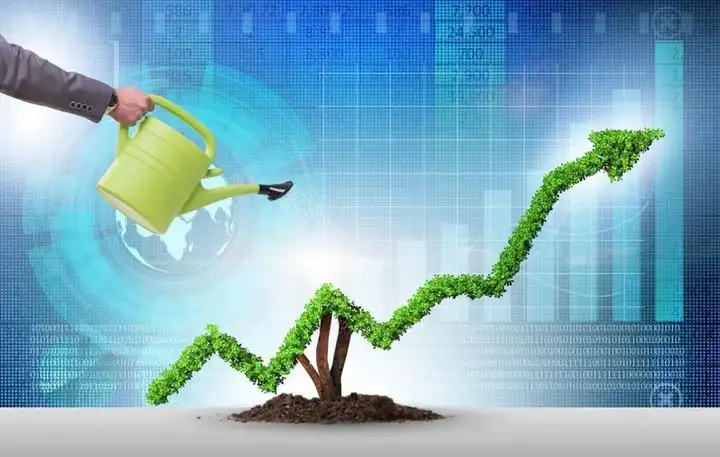
一、現(xiàn)場管理的革命性工具
1. 5S可視化革命 某汽車零部件廠通過5S管理,使工具尋找時間從日均47分鐘降至8分鐘,僅此一項年節(jié)省工時成本超200萬元。其核心在于:整理(Seiri)清除30%冗余物品,整頓(Seiton)實施影子板定位工具,清掃(Seiso)建立設(shè)備點檢標準,清潔(Seiketsu)制定可視化看板,素養(yǎng)(Shitsuke)形成持續(xù)改進文化。
2. 全員生產(chǎn)維護(TPM) 青島某電子廠導(dǎo)入TPM后,設(shè)備綜合效率(OEE)從65%提升至89%。關(guān)鍵實施步驟:
-
制定設(shè)備清掃-點檢-潤滑標準化流程
-
建立異常預(yù)警的物聯(lián)網(wǎng)監(jiān)測系統(tǒng)
-
操作工與維修團隊聯(lián)合開展焦點改善
-
實施故障樹分析(FTA)預(yù)防重大停機
二、流程優(yōu)化的核心技術(shù)
3. 價值流深度分析 某衛(wèi)浴企業(yè)通過繪制現(xiàn)狀價值流圖,發(fā)現(xiàn)38%的工序不增值。實施對策:
-
合并3個分散的質(zhì)檢工序為在線檢測站
-
將批量運輸改為AGV小車連續(xù)流配送
-
建立工序間1:1生產(chǎn)節(jié)拍平衡
最終在制品庫存降低72%,場地占用減少500㎡。
4. SMED快速換模系統(tǒng) 注塑企業(yè)應(yīng)用SMED方法將換模時間從120分鐘壓縮至23分鐘:
-
分離內(nèi)外部作業(yè)(模具預(yù)熱提前完成)
-
采用液壓快換系統(tǒng)替換螺栓緊固
-
開發(fā)專用工具車實現(xiàn)"所有工具觸手可及"
-
錄制標準作業(yè)視頻培訓(xùn)多能工
5. 單元化柔性生產(chǎn) 某醫(yī)療器械公司將傳統(tǒng)流水線改造為U型單元,實現(xiàn):
-
生產(chǎn)周期從7天縮短至8小時
-
人工減少40%但產(chǎn)能提升25%
-
切換產(chǎn)品型號時間降至15分鐘
關(guān)鍵要素包括:多工序集成、站立式作業(yè)、物料"水蜘蛛"配送、ANDON異常呼叫系統(tǒng)。
三、組織防錯:構(gòu)建"人機共防"生態(tài)
6. Poka-Yoke防錯技術(shù) 某變速箱工廠通過三級防錯網(wǎng)絡(luò)將缺陷率降至12PPM:
-
初級防錯:治具定位銷防止錯裝
-
中級防錯:扭矩槍聯(lián)網(wǎng)監(jiān)控,超差自動鎖止
-
高級防錯:視覺檢測系統(tǒng)實時攔截不良品典型應(yīng)用場景包括錯裝預(yù)防、漏工序檢測、參數(shù)防呆等。
7. 標準化作業(yè)體系 世界500強食品企業(yè)建立包含2174份標準作業(yè)書的體系,確保:
-
新員工3天達到標準產(chǎn)能
-
不同班次效率波動控制在±2%以內(nèi)
-
改善提案實施后48小時內(nèi)更新標準
核心要素:時間觀測、動作分析、標準三票(作業(yè)/檢驗/物流)、動態(tài)更新機制。
四、供應(yīng)鏈協(xié)同創(chuàng)新
8. 看板拉動系統(tǒng) 某白色家電企業(yè)實施電子看板后:
-
庫存周轉(zhuǎn)率從5次提升至11次
-
缺料停工時間下降83%
-
供應(yīng)商交貨周期壓縮40%
創(chuàng)新點在于:將傳統(tǒng)看板升級為智能物聯(lián)網(wǎng)系統(tǒng),實現(xiàn)供應(yīng)商-物流-生產(chǎn)實時聯(lián)動。
9. 戰(zhàn)略供應(yīng)商協(xié)同開發(fā)
工程機械龍頭與核心供應(yīng)商共建VAVE(價值分析與價值工程)團隊,年度降本達采購額的3.8%。主要措施:
-
聯(lián)合設(shè)計簡化結(jié)構(gòu)的連接件
-
開發(fā)通用化模塊降低SKU數(shù)量
-
共享產(chǎn)能數(shù)據(jù)實現(xiàn)JIT交付
-
建立成本透明化的利潤分成機制
五、持續(xù)改進的永動機
10. 改善提案制度 豐田全球每年收到200萬條員工建議,實施率超85%。某民營制造企業(yè)借鑒后:
-
設(shè)立改善積分商城,1個金點子=200元購物券
-
每周"改善擂臺賽"展示最佳實踐
-
建立改善道場培訓(xùn)問題解決七步法
-
將改善成果納入晉升考核指標
兩年內(nèi)實現(xiàn)人均年提案4.6件,累計降本超3800萬元。
(結(jié)語) 從日本豐田到德國博世,從美國丹納赫到中國海爾,這些精益標桿企業(yè)的實踐印證:成本控制不是簡單的砍預(yù)算,而是通過系統(tǒng)性的價值重構(gòu)實現(xiàn)持續(xù)進化。
十大策略的協(xié)同應(yīng)用,將幫助企業(yè)構(gòu)建"消除浪費-質(zhì)量保障-柔性響應(yīng)"三位一體的競爭力護城河。正如精益大師詹姆斯·沃麥克所言:"精益不是降低成本的方法,而是創(chuàng)造價值的新范式。"
當下正是企業(yè)啟動精益轉(zhuǎn)型的最佳時機,因為最大的成本,永遠是停滯不前的機會成本。