IE起源于美國,但在日本得到了最深刻的踐行、因此才導致了豐田生產(chǎn)方式TPS及“精益制造”LP的誕生。如今IE已經(jīng)在全世界得到了認可與運用,成為消除浪費的“精益利器”
IE經(jīng)過過年的專業(yè)研究與企業(yè)踐行,已經(jīng)取得了長足的發(fā)展,從實戰(zhàn)的高度、廣度、深度來看可以區(qū)分為基礎階段(生產(chǎn)單元改善)、提升階段(生產(chǎn)方式革新)、深入階段(VSM分析與全流程優(yōu)化)。如果沒有掌握VSM分析,企業(yè)的改善只能停留在點或線的范圍,不能診斷與識別全流程端to端的浪費,也就無法全格局地實施流程優(yōu)化。所以VSM不僅需要IE工程師牢牢掌握,更需要企業(yè)的各級人員、特別是中高層管理人員深刻理解并在實踐活動中率先示范。不運用VSM,IE的精益改善始終有點“井底之蛙”之感
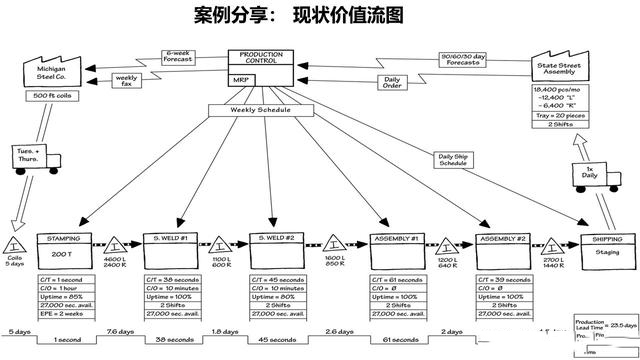
一、認知VSM價值流圖 1、 價值流圖VSM的起源 ? 美國學者M.羅瑟與J.舒克教授在名著《學習觀察》中首次提出了價值流圖VSM的概念,并發(fā)表了著名宣言:哪里為客戶提供產(chǎn)品與服務,哪里就有價值流,其間一定有浪費,挑戰(zhàn)在于如何觀察,找出浪費!
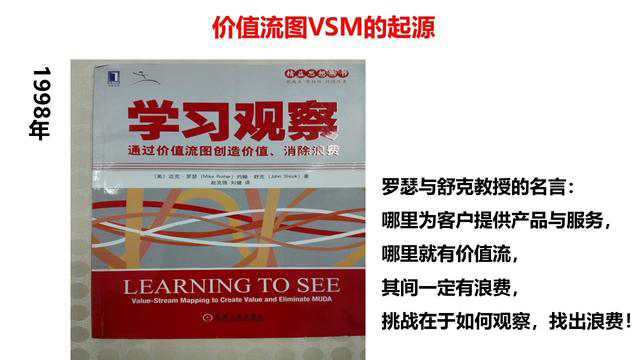
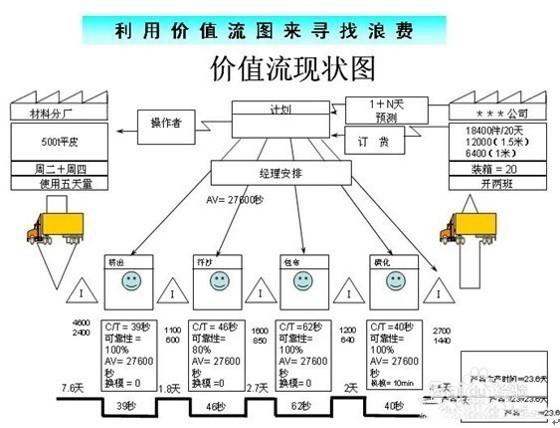
2、 價值流圖VSM的內(nèi)涵
? 價值流圖(value stream mapping)是用一張紙、一支筆順著物料和信息的流程收集關鍵數(shù)據(jù),表示一件產(chǎn)品從訂單到交付全過程(端to端),每一個工序的物料流和信息流的圖表,并進行定量分析的工具
? 兩大一級流程的數(shù)據(jù)收集與表達
- 產(chǎn)品實現(xiàn)的工藝物料流
- 訂單實現(xiàn)的指令信息流
3、 價值流圖VSM的用途
? 價值流圖有助于全面、全過程觀察和理解產(chǎn)品,通過價值流過程的物料流動和信息流動,特別是其中的增值和非增值(浪費)活動,從而發(fā)現(xiàn)浪費和確定需要改善的地方,更容易找出問題所在
? 價值流圖還可以避免只應用個別的精益工具,進行局部、孤立的改善(工序IE改善、工藝PE改善)。通過繪制現(xiàn)狀圖,設計理想狀態(tài)圖并盡快付諸實施,通過這種方法,可以全面地改善價值流(點、面、流程全體),從而為客戶、協(xié)作商和供應商帶來最大的利益
4、 價值流圖VSM的目標
? 價值流圖是一種強力的可視化工具,它的主要目標是幫助我們確認運營流程中存在的潛在的(隱形的),對客戶不增值的浪費活動
? 價值流圖是任何企業(yè)展開流程分析的有效工具,既可作為企業(yè)內(nèi)部溝通的工具,也可作為企業(yè)的戰(zhàn)略規(guī)劃工具
? 將企業(yè)流程所有相關的物流、信息流和現(xiàn)金流以圖示的方式加以表達,有利于企業(yè)了解目標的經(jīng)營現(xiàn)況和未來的經(jīng)營現(xiàn)況
? 繪制一副現(xiàn)有系統(tǒng)的整體價值流程圖,可以讓所有人一致看出流程中的浪費情形, 未來面貌的的價值流程圖可顯示期望實現(xiàn)的未來遠景,并有助于識別出價值流程中最能減少浪費情形的機會
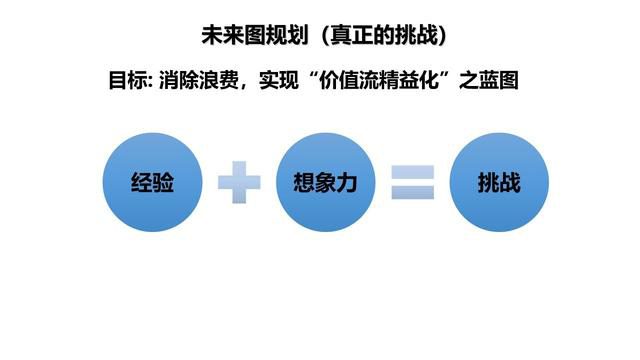
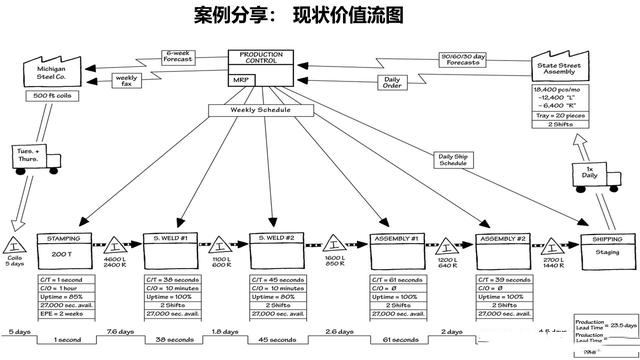
借助它,你可以找到最明顯的5-10產(chǎn)生大量浪費的步驟,并開始著手制定消除浪費的計劃并加以執(zhí)行
二、繪制VSM價值流圖
1、價值流圖分為4個層別,可以從最簡單的“點”(生產(chǎn)單元)入手、但有必要延伸至“線”(車間)及“面”(制造全流程),優(yōu)秀的企業(yè)還將擴展至“鏈”(核心供應商以及核心銷售商、代理商),被稱為“價值鏈優(yōu)化”
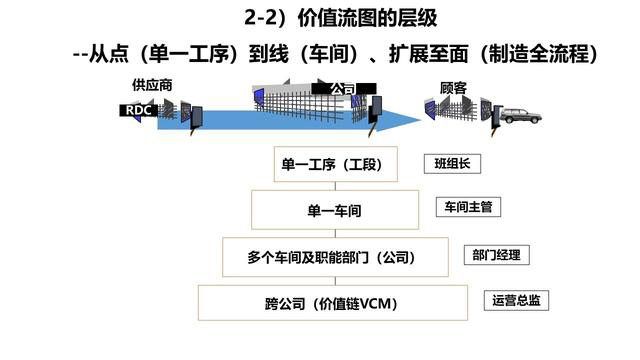
價值流圖的層別進化
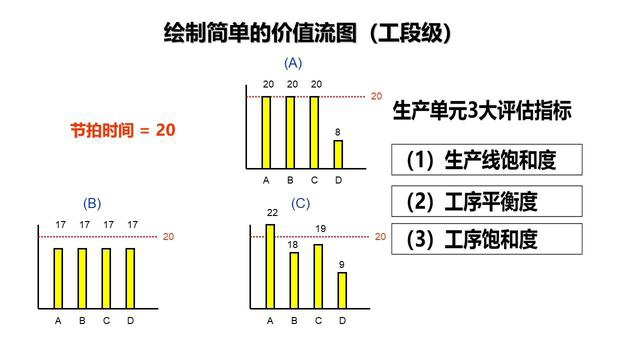
工段級VSM
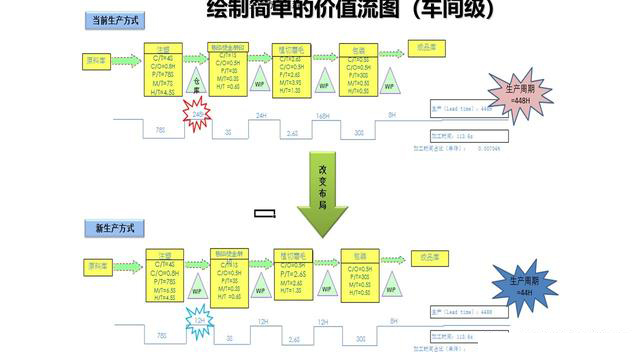
車間級VSM
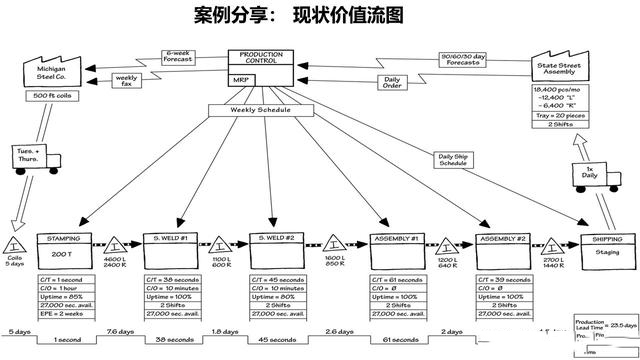
制造全流程VSM
2、繪制步驟
? 價值流圖的基本特點
- 使用專用圖標
- 2個流(物料流、信息流)
- 物料流:下半部分、從左到右
- 信息流:上半部分、從右到左
- 3層結(jié)構(gòu)(部門、工段流程、時間線)
- 定量化數(shù)據(jù)
- 數(shù)據(jù)化評估
? 繪制第一層
- 畫客戶,供應商(協(xié)作商)和生產(chǎn)控制
- 輸入客戶需求(客戶數(shù)據(jù)箱):客戶原點,決定下游的節(jié)拍
- 計算每天的產(chǎn)量和包裝箱需求
- 畫出外向物流及其頻率
- 畫出內(nèi)向物流及其頻率
? 繪制第二層
- 從左到右添加工序(工段)框。有分叉流程時,使用并行排列
- 添加數(shù)據(jù)箱
- 添加信息流,標注其方式、內(nèi)容和頻率。“從右至左”、“從上至下”
- 搜集工藝屬性并填寫數(shù)據(jù)
- 標注操作工數(shù)量
- 添加庫存位置、數(shù)量,并折算其周期時間
- 庫存產(chǎn)生的原因不同,其折算周期時間的算法也不盡相同
- 畫出推動,拉動,先進先出等物料流圖標。“從左至右”
- 添加其它認為必要的信息
? 繪制第三層
- 增加工作時間
- 把VA及所有NVA時間對應到時間線上
- 計算工廠交付周期(L/T)和總增值時間(VCT)
三、運用VSM優(yōu)化價值流
1、關鍵步驟一:價值流診斷與分析
? 價值流診斷與分析是建立在價值流圖基礎之上的有效分析工具,它起源于豐田公司的“材料及信息流分析”(MIFA)
? 任何的生產(chǎn)過程中均存在著材料流和信息流,價值流分析是從為客戶創(chuàng)造價值的視角,將我們的注意力傾注于建立流動、消除非增值活動、快速增加價值的改善上去,并建立起材料流和信息流的聯(lián)系
? 借助價值流圖的價值流分析,是有效的”學會發(fā)現(xiàn)“的手段
- 定量計算與診斷現(xiàn)狀流程中的“價值創(chuàng)造率”
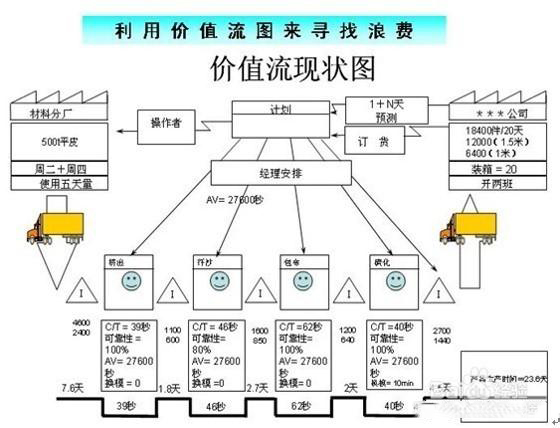
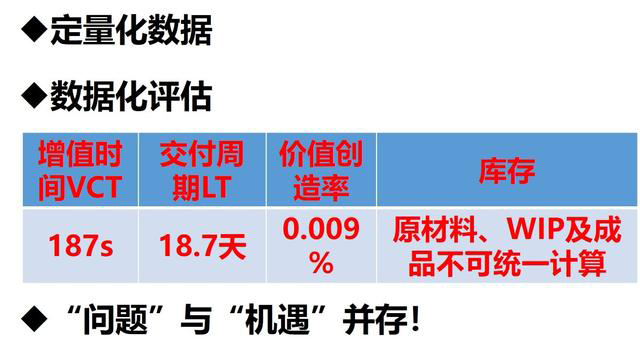
? 價值流分析用于觀察和理解流程的現(xiàn)狀同時繪制實施精益的未來藍圖,并定量評估流程優(yōu)化后的“指標性提升”
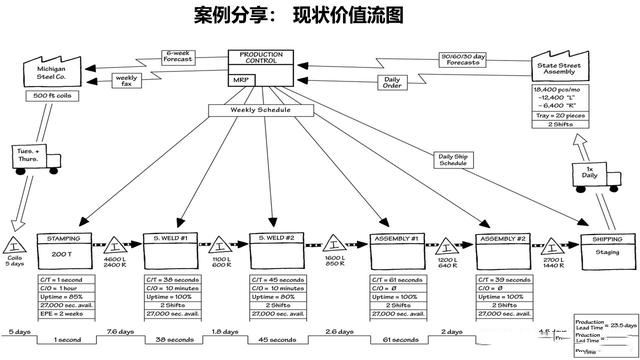
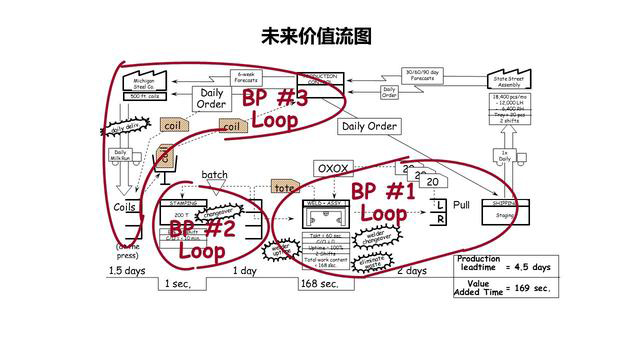
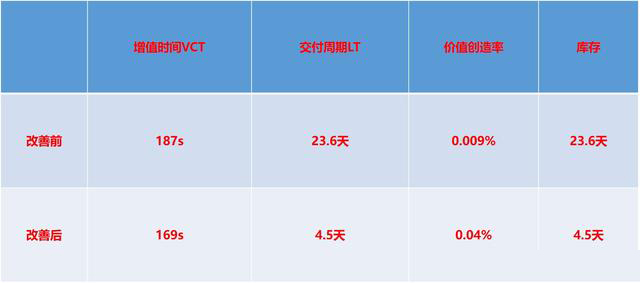
? 我們都可以發(fā)現(xiàn),只要一切從客戶的需要出發(fā),積極運用企業(yè)內(nèi)部及外部的各種資源,我們就能夠發(fā)現(xiàn)、創(chuàng)造、傳遞更多的價值
? 客戶價值流,就如同企業(yè)另一套貫穿內(nèi)外的循環(huán)系統(tǒng),為企業(yè)發(fā)展提供源源不斷的能量,
? 精益的企業(yè)會將價值流分析擴展延伸到外部“供應商”及“協(xié)作商”(價值鏈管理VCM)
? 孤立地運行繪圖是遠遠不夠的,如果不能很好地理解精益生產(chǎn)的原則,那么繪制圖形不會比早期和中期那些改進的工作車間更接近使浪費最小化并取得極好效果的目標
2、關鍵步驟二:價值流精益優(yōu)化
精益優(yōu)化思路一:杜絕過盈生產(chǎn)
? 過盈生產(chǎn): 過多生產(chǎn)或過早生產(chǎn)
? 過盈生產(chǎn)會導致嚴重的后果
- 不必要的空間需求
- 額外的工時,搬運和分類
- 返工風險
- 庫存風險
精益優(yōu)化思路二:準時生產(chǎn)JIT
在當今“多品種、小批量、快交期、低庫存、高品質(zhì)”的市場與客戶需求時代,未來不再是”大魚吃小魚“的規(guī)模競爭而是”快魚吃慢魚“的速度競爭,與時間的競爭成為企業(yè)的”第三極競爭力“。傳統(tǒng)大批量制造模式已經(jīng)成為企業(yè)競爭力的嚴重障礙,必須徹底革新!
而源于豐田的準時生產(chǎn)JIT理念正在以新的制造模式與科技革新浪潮引領著人類的制造業(yè)奔向“柔性靈敏制造”
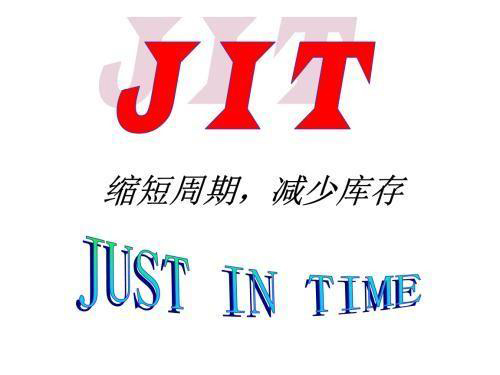
精益優(yōu)化核心課題
? “產(chǎn)品實現(xiàn)流程”的快速化
- 徹底革新“傳統(tǒng)大批量制造模式“、導入”精益流動式制造模式“,大幅短縮制造周期Lead Time
- 大幅消除制造流程中的”等待“與”搬運“浪費
- 推行頻繁、快速換型(SMED),實現(xiàn)全品種混流化生產(chǎn)Hybrid
- 制造全流程、各個工段之間實行“拉動式”
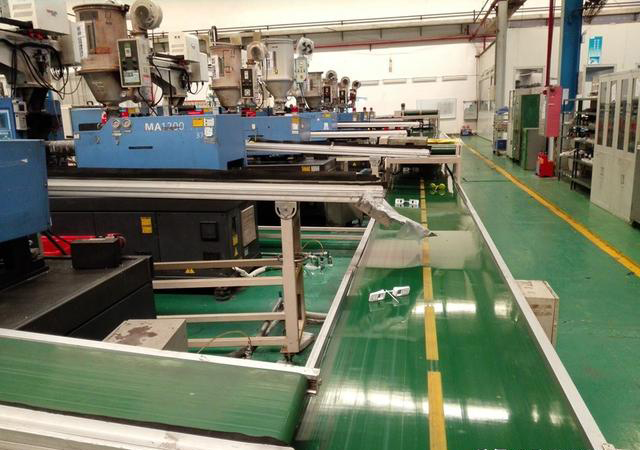
流動式單件流生產(chǎn)
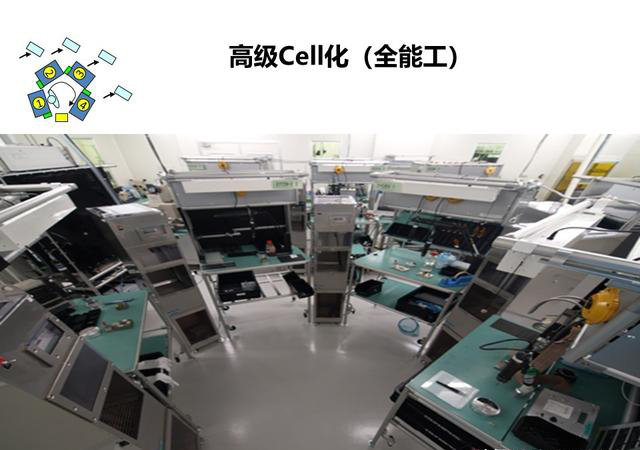
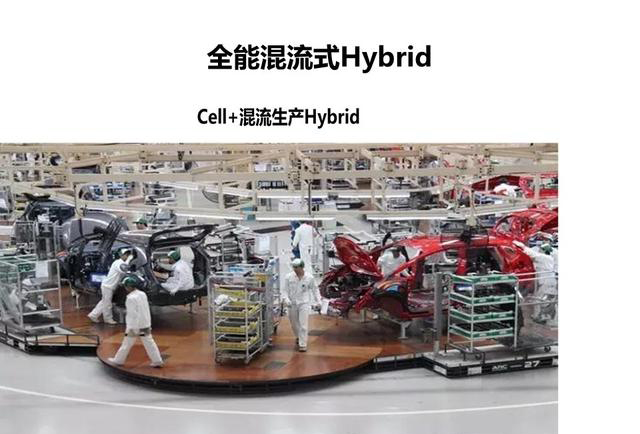
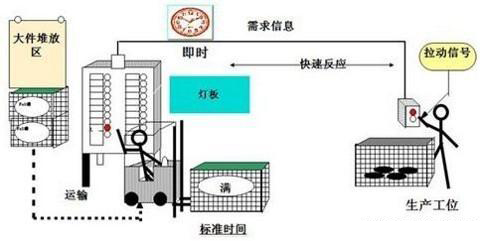
? “訂單實現(xiàn)流程”的準時化JIT
- 強化PMC職能的權威、提升PMC的價值存在
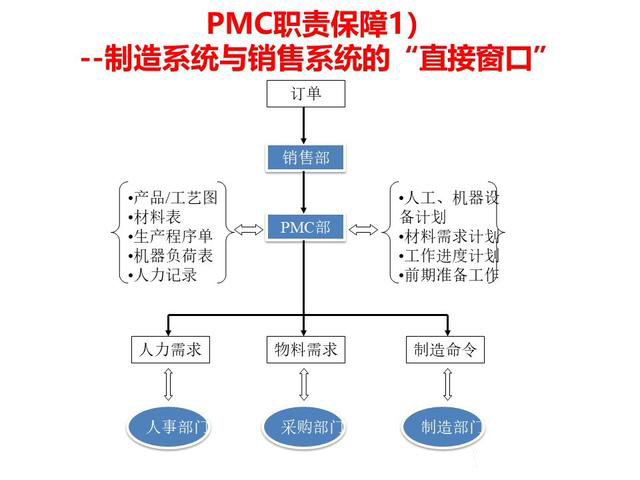
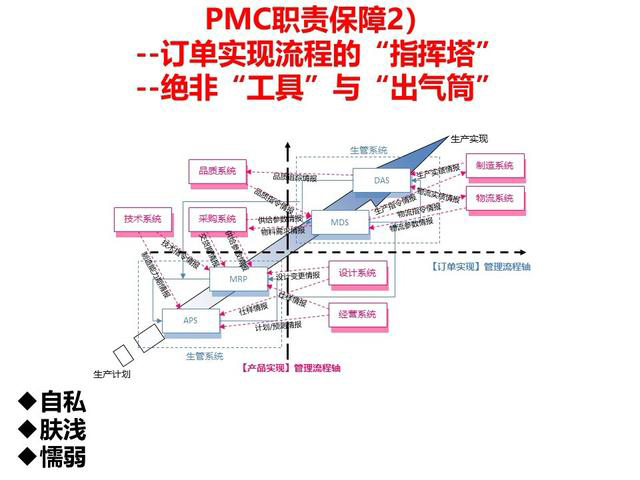
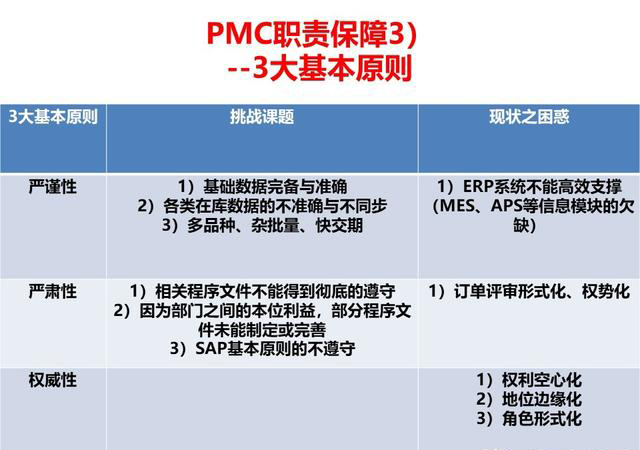
- 建立產(chǎn)、供、銷聯(lián)動的PSI計劃體系
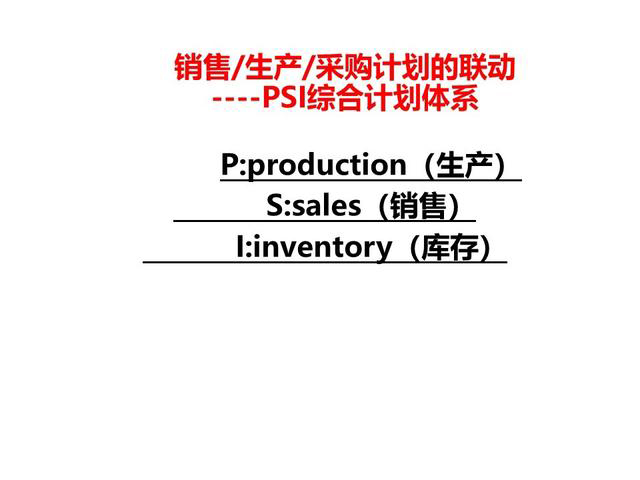
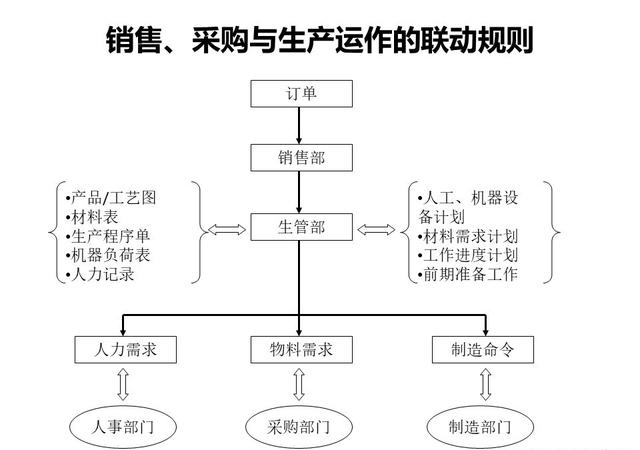
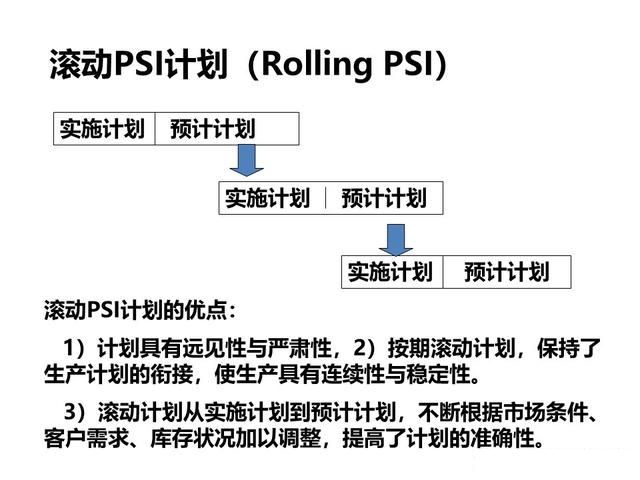
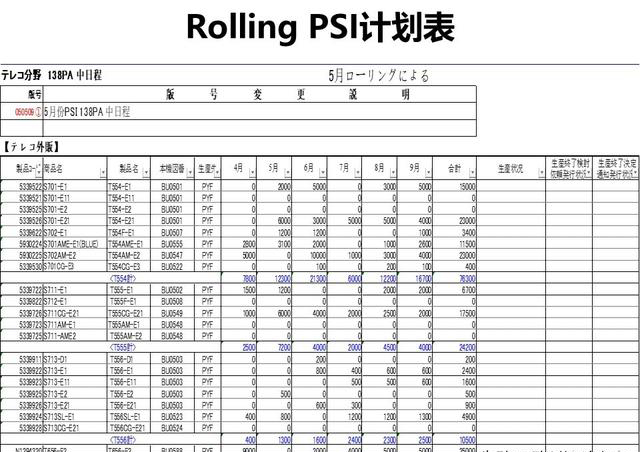
- 擴容ERP系統(tǒng)功能、導入MES與APS
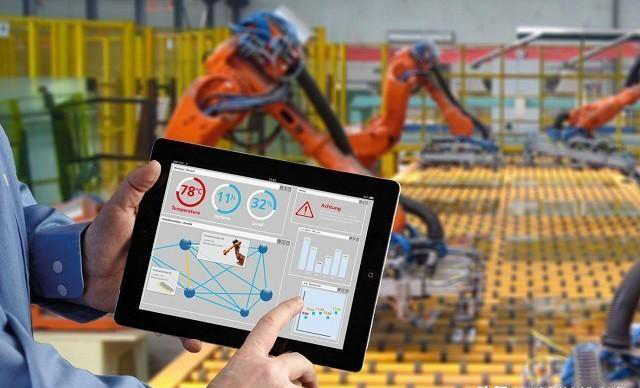
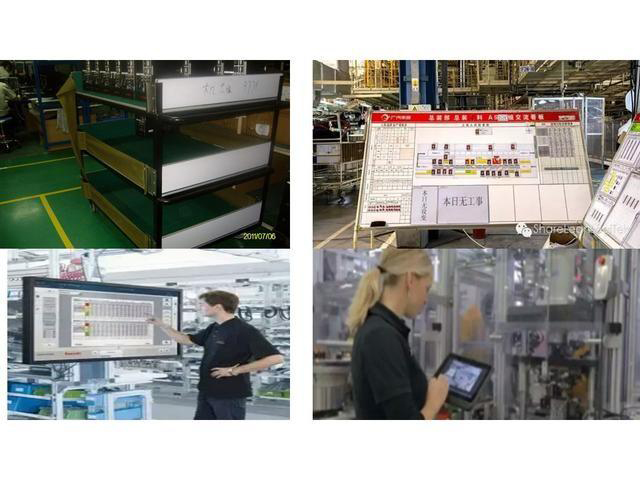
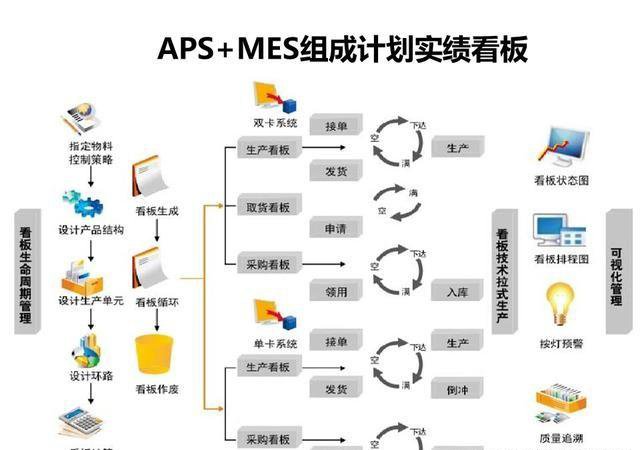
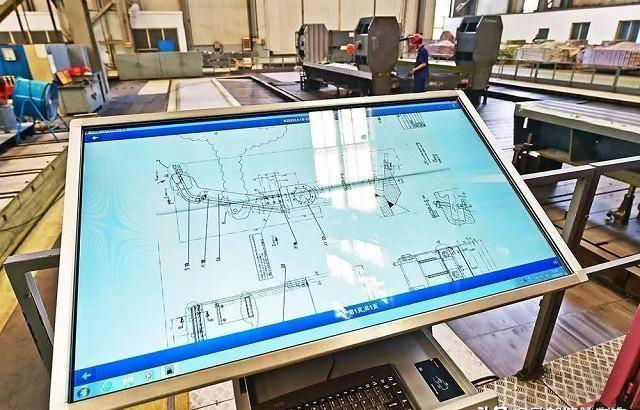
- 構(gòu)建核心供應商的“戰(zhàn)略聯(lián)盟、互利共生“戰(zhàn)略,運用VSM、JIT手段實現(xiàn)快速供貨
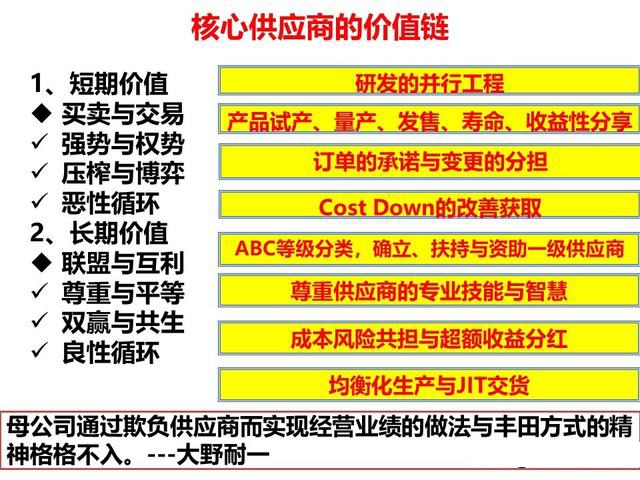