精益生產(chǎn)的目的就是消除一切浪費(fèi),降低成本,向零缺陷、零庫(kù)存進(jìn)軍,用最少的投入實(shí)現(xiàn)最大的產(chǎn)出,實(shí)現(xiàn)利潤(rùn)最大化。
目前生產(chǎn)企業(yè)的產(chǎn)品由供不應(yīng)求轉(zhuǎn)變到供大于求,企業(yè)要持續(xù)經(jīng)營(yíng)下去,必須讓企業(yè)有利潤(rùn)回報(bào)?,F(xiàn)實(shí)模式是"利潤(rùn)=售價(jià)-成本”。模式是講商品價(jià)格是由市場(chǎng)決定的,而非源于企業(yè)的內(nèi)部,在這種條件下,要想擴(kuò)大利潤(rùn)就必須讓成本更小,這種營(yíng)銷思維是買方市場(chǎng)的產(chǎn)物。對(duì)于國(guó)民經(jīng)濟(jì)的主體制造業(yè),希望通過(guò)精益生產(chǎn)活動(dòng),一方面實(shí)現(xiàn)企業(yè)實(shí)效的持續(xù)增長(zhǎng),另外一方面幫助企業(yè)人員提升精益管理能力,使企業(yè)有‘造血’能力,經(jīng)過(guò)持續(xù)三至五年的精益生產(chǎn)推進(jìn)活動(dòng),將企業(yè)打造成行業(yè)標(biāo)桿!
實(shí)際精益生產(chǎn)推進(jìn)中,確實(shí)有很多企業(yè)通過(guò)精益生產(chǎn)提升企業(yè)競(jìng)爭(zhēng)力的成功案例,比如德昌電機(jī)、美的電器、格力電器等,但是也有很多企業(yè)推行不成功的案例,基本上五大原因:死因一之“拖延”;死因二之“缺乏‘人性’領(lǐng)導(dǎo)力”;死因三之“脫離現(xiàn)場(chǎng)”;死因四之“瞻前顧后、優(yōu)柔寡斷”;死因五之“沒(méi)有持續(xù)改善”。這五大原因都關(guān)聯(lián)到了改善課題的選定。通常我們精益改善如下圖所示:
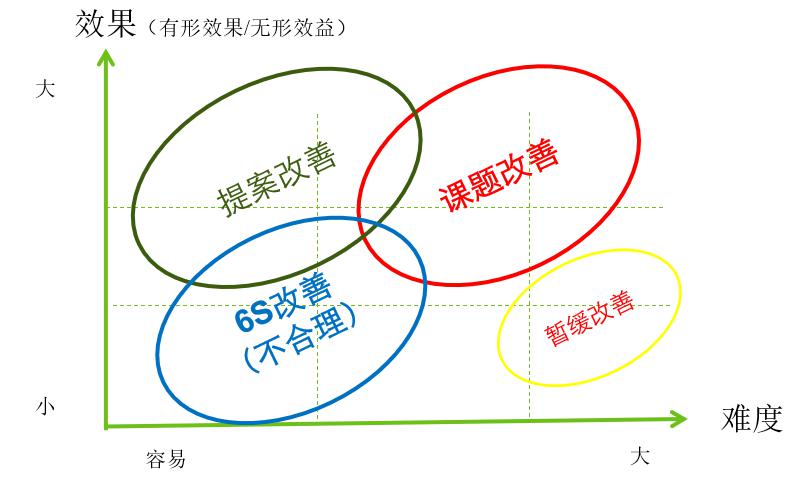
精益生產(chǎn)導(dǎo)入初期先是針對(duì)6S難度小直接回報(bào)低的項(xiàng)目進(jìn)行改善,然后擴(kuò)展到數(shù)據(jù)分析后難度小回報(bào)大的提案進(jìn)行改善。再之后,隨精益生產(chǎn)推進(jìn),日常生產(chǎn)中的疑難問(wèn)題被識(shí)別出,為主要浪費(fèi),通過(guò)個(gè)人或單個(gè)部門難以解決;同時(shí)這些問(wèn)題會(huì)分布在產(chǎn)品品質(zhì)、生產(chǎn)成本、產(chǎn)品交期以及6s的疑難問(wèn)題(半制品三定關(guān)聯(lián)到布局、JIT、自働化),都為等待改善的問(wèn)題點(diǎn),以怎么樣的的優(yōu)先順序?qū)嵤┱n題改善呢?這沒(méi)有固定模式,但這是左右企業(yè)推行精益成敗的關(guān)鍵,我認(rèn)為需要考慮如下幾個(gè)方面:
一、結(jié)合公司未來(lái)三至五年的營(yíng)運(yùn)戰(zhàn)略,識(shí)別出在哪些方面需要補(bǔ)強(qiáng)的內(nèi)容?選定該方向的課題導(dǎo)入,能使精益生產(chǎn)同公司戰(zhàn)略保持一致;
二、當(dāng)前實(shí)際生產(chǎn)中,收集產(chǎn)品品質(zhì)方面(不良減少;檢查效率改善;供應(yīng)商質(zhì)量改善;)、生產(chǎn)成本方面(設(shè)備效率改善;勞動(dòng)生產(chǎn)率改善;材料等投入損耗減少;各類損耗減少;失敗成本降低;)、產(chǎn)品交期方面(計(jì)劃達(dá)到率改善;生產(chǎn)周期縮短;)、現(xiàn)場(chǎng)6s(垃圾分類處理和資源再利用;節(jié)能降耗活動(dòng);事故、災(zāi)害消滅活動(dòng))中的疑難瓶頸點(diǎn),識(shí)別出影響占比比較大的前幾項(xiàng)內(nèi)容,針對(duì)這些痛點(diǎn)我們使用課題改善,按八大步驟獲得收效會(huì)因?yàn)槠款i的改善而收效顯著,同時(shí)一些精益生產(chǎn)的相關(guān)工具通過(guò)實(shí)踐,小組成員容易撐握并在現(xiàn)場(chǎng)固化;
三、一個(gè)企業(yè)從導(dǎo)入精益生產(chǎn)開始,到形成企業(yè)精益生產(chǎn)文化,一般需要三到五年的時(shí)間。相關(guān)的管理模塊有:精益人效管理、精益設(shè)備管理(TPM)、精益成本管理、精益品質(zhì)管理、生產(chǎn)計(jì)劃管理、精益流程管理、精益文化及人才培養(yǎng)。整個(gè)三年以上精益生產(chǎn)活動(dòng)計(jì)劃要有總規(guī)劃,然后具體到每一年要導(dǎo)入哪幾個(gè)管理模塊?相應(yīng)模塊的哪些內(nèi)容?這樣每年課題雖然是以不同點(diǎn)的方式進(jìn)行,但通過(guò)三到五年的課題改善落實(shí),就形成了公司精益生產(chǎn)活動(dòng)體系;
四、選定課題項(xiàng)目的難易程度要適中,我們要考慮到整個(gè)項(xiàng)目時(shí)間4-6個(gè)月,成員剛開始對(duì)精益生產(chǎn)是一學(xué)習(xí)接受的過(guò)程,課題過(guò)難讓大家對(duì)課題改善失去了興趣。當(dāng)然收益回報(bào)也是其中要重點(diǎn)考慮的內(nèi)容;
五、課題選定時(shí)要求考慮課題負(fù)責(zé)人,精益生產(chǎn)推行一般是公司戰(zhàn)略層面導(dǎo)入的。導(dǎo)入初期公司各部門長(zhǎng)是精益活動(dòng)推行成敗的關(guān)鍵,因此初期項(xiàng)目負(fù)責(zé)人是各部門長(zhǎng),隨著精益生產(chǎn)的推行,第二年及以后可以由下面的部下主管擔(dān)任責(zé)任人。在課題選定前需對(duì)目前公司的人才儲(chǔ)備進(jìn)行一快速梳理,按照三年精益生產(chǎn)規(guī)劃,公司部門人才資源是否足夠,有怎樣人才儲(chǔ)備計(jì)劃支持?相關(guān)人員應(yīng)進(jìn)入下面知識(shí)模塊學(xué)習(xí):品質(zhì)的不良品改善、來(lái)料供應(yīng)鏈的管理、設(shè)備的自主保全改善、MTBF/MTTR改善、OEE/SMED改善、VSM/ONE PIECE FLOW、生產(chǎn)線的在制品(WIP)降低及布局LAYOUT優(yōu)化、生產(chǎn)線的節(jié)拍TT及線平衡LOB、備品備件成本降低、車間成本數(shù)據(jù)及控制、生產(chǎn)計(jì)劃達(dá)成改善、能源成本控制等,整個(gè)人才學(xué)習(xí)規(guī)劃需要有公司層面計(jì)劃;
精益生產(chǎn)推進(jìn)中正確的課題選定及改善除給公司帶來(lái)業(yè)績(jī)回報(bào)收益外,我們通過(guò)建立以大班組為單元的改善小組,從樣板區(qū)打造到卓越現(xiàn)場(chǎng)推進(jìn),包括課題活動(dòng)都是通過(guò)看板方式展現(xiàn)出來(lái)的。這樣課題活動(dòng)也給公司培養(yǎng)了人才,建立一個(gè)學(xué)習(xí)型組織。通過(guò)每個(gè)課題的點(diǎn),經(jīng)過(guò)三年推進(jìn),使精益生產(chǎn)管理的不同模塊真實(shí)熔入到公司實(shí)際生產(chǎn)過(guò)程中。我們的產(chǎn)品品質(zhì)、成本、交期以及我們的管理團(tuán)隊(duì),通過(guò)精益生產(chǎn)課題活動(dòng)在行業(yè)中形成強(qiáng)大競(jìng)爭(zhēng)力。